Microencapsulation of phase change materials – Generation 4.0 customized for your needs
Phase change materials must be contained in one form or another to be of any repeatable and beneficial use as temperature regulators. In certain applications, such as textiles, microencapsulated phase change materials (microPCMs) are the only appropriate containment system.
By Monte C. Magill
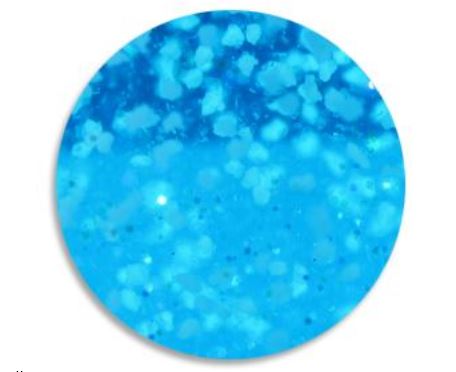
Phase change materials (PCMs) are used to regulate temperature in a variety of applications. PCMs can be contained in hard packs, soft packs, pouches, spheres, tubes and even large tanks. PCMs contained in those ways can be used in HVAC systems, wallboard, shipping containers, beverage coolers, food warmers, cooling vests, refrigerators, freezers and infant incubators.
Some applications, however, require microscopic containment to ensure product performance. Microencapsulated phase change materials, known as microPCMs, help make sure that products such as jackets and bedding maintain the flexibility expected of them. The cushioning properties of memory foam mattresses, for example, are unaffected when microPCMs are incorporated into the foam matrix itself. And microPCMs are used in wallboard because they will not leak when the wallboard is cut or pierced by screws or nails.
So, what is microencapsulation? How are microcapsules made? In general, microencapsulation is the process of forming a shell around a small particle, usually less than 1000 microns, of any core material. For PCMs, the particles are usually less than 50 microns, the diameter of a thin human hair. The process of making microcapsules can be either a physical process, as with spray drying and Wurster bed coating, or a chemical process, as is most commonly used to make microPCMs. This paper will focus on the latter.
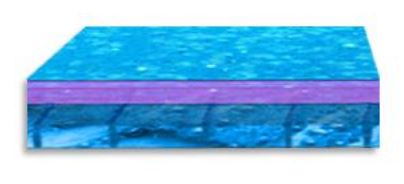
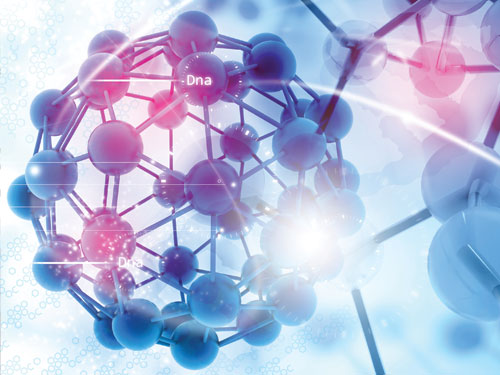
Most microencapsulation is done with the intent of releasing its contents upon some trigger mechanism, such as pressure for carbonless microcapsules, scratching for scratch-and-sniff stickers, digestion for enteric coatings of medicinal products and heat for fragrances used in dryer sheets. However, microPCMs are intended to contain their core material permanently, no matter what forces they are exposed to. Liquid crystals and thermochromatic pigments are the only other materials whose microencapsulation is intended to be permanent.
The two main shell materials used for microPCMs are melamine-formaldehyde (MF) and acrylic. The MF shell gives a very durable shell but carries the stigma of its formaldehyde component, a known carcinogen. Because they come in contact with skin, nearly all bedding and apparel products that contain microPCMs have acrylic shell microcapsules.
The two processes have a lot in common. Both are water-based operations in which an oil-in-water emulsion process (a combination of high shear force and emulsifiers) is used to create the small particle size desired, in some cases just several microns in diameter. The two methods differ in that the MF process starts with both wall-forming components in the water phase and uses a combination of lower pH and higher heat to form the shell polymer. The acrylic shell process begins with one wall-forming component in the core and the other in the water phase and the shell polymer is formed by various combinations of added catalysts, pH adjustment and heat.
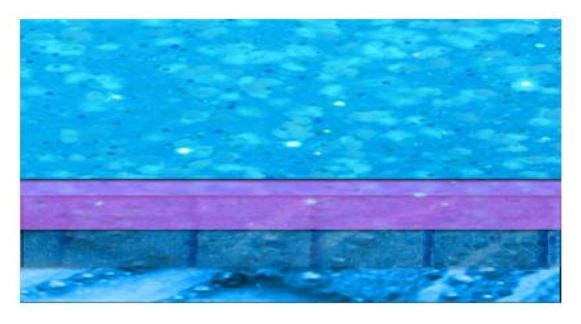
In either case, the core-to-shell ratio can be from 60:40 to 95:5, with the most typical being 80 to 85 percent core and 20 to 15 percent shell. These microPCMs can then be available as a slurry (from about 20 to 45 percent microPCMs in water), as a filter cake (water removed to obtain a moist cake between 50 and 75 percent microPCMs and the rest water) or as a dry, free-flowing powder (usually via spray drying).
A variety of quality-control tests can be conducted on finished microPCMs. They are:
- Differential scanning calorimeter: DSC tests the amount of energy required to heat or cool a sample (usually between 5 to 10 milligrams in size). An example of a DSC chart is below. It will yield critical information about a material’s melt and crystallization points and widths, the amount of energy or latent heat it has at phase change temperatures and if there is any noteworthy supercooling (a crystallization point/melt point difference of usually greater than 10°C).
- Particle size analysis: This test measures the particle size both in range and on average and can be done by microcapsule count or by microcapsule volume.
- Free oil: This test is usually done as a solvent extraction and weight analysis method and/or with a gas chromatogram (GC).
- Thermogravimetric analysis: TGA measures the weight loss of a sample of the microPCMs as the temperature increases. This is a quasi-analysis of the strength of the microPCMs since it essentially measures the microcapsule shell’s resistance to bursting as its core builds up enough vapor pressure to tear the microcapsule open, much like moisture escaping from a kernel of corn as it pops.
About the author
Monte Magill has been working with microencapsulated phase change materials since 1992. He spent over a decade helping to bring Outlast Technologies from a small startup to a world leader in temperature-regulation technology for textiles. His work with phase change materials also includes stints in business development for Renewable Alternatives, Entropy Solutions’ research and development laboratory in Tuscaloosa, Ala. He lives near Boulder, Colo.